Understanding Screen Mesh Count and Its Impact on Print Quality
Understanding Screen Mesh Count and Its Impact on Print Quality
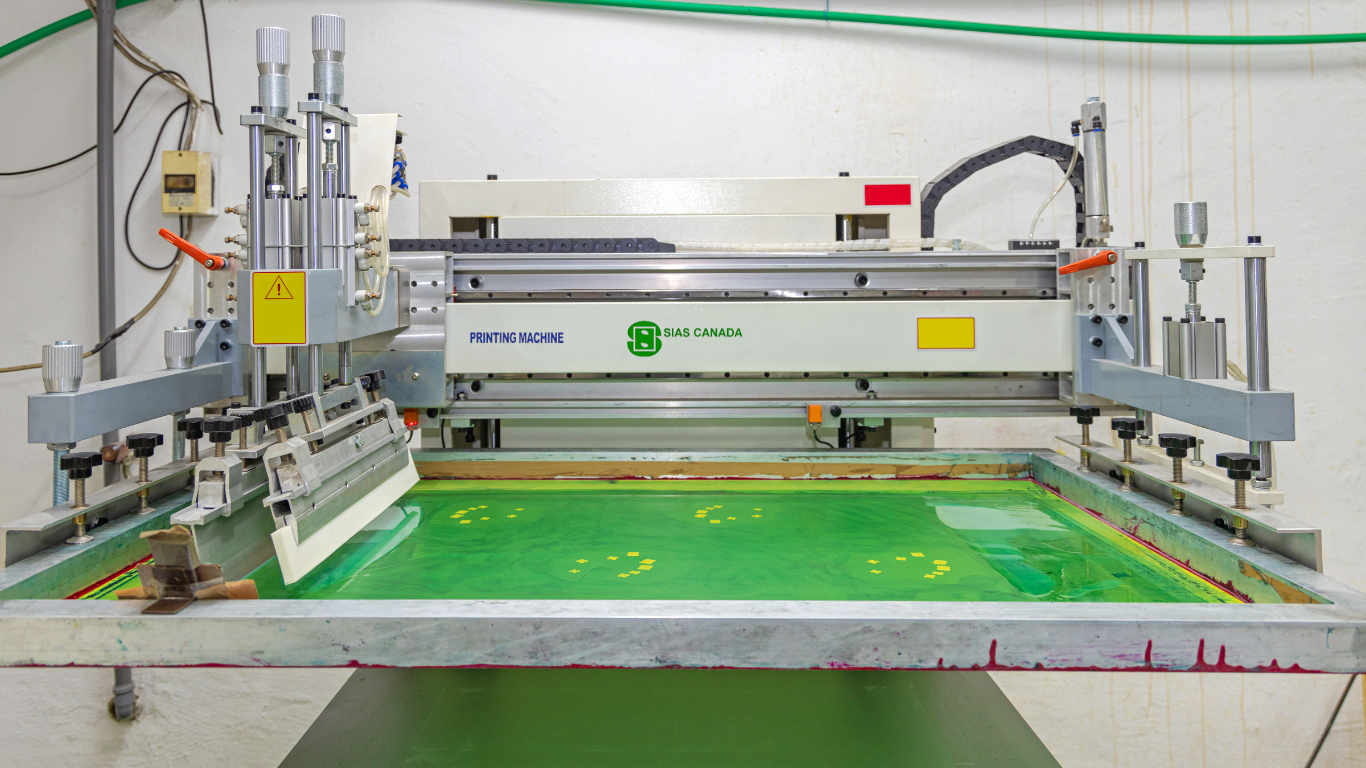
In screen printing, one of the most crucial factors that affect the quality and detail of the final print is the screen mesh count. The mesh count refers to the number of threads per inch in the screen fabric. Understanding and selecting the appropriate mesh count is essential for achieving the desired print outcome, as it influences ink deposition, detail reproduction, and the overall look of the print. In this post, we'll delve into what screen mesh count is, how it impacts print quality, and how to choose the right mesh count for different applications.
What Is Screen Mesh Count?
Screen mesh count indicates the density of threads in the screen fabric, measured as the number of threads per linear inch. For example, a 110 mesh screen has 110 threads per inch, while a 305 mesh screen has 305 threads per inch. The mesh count directly affects the size of the openings between the threads, determining how much ink passes through the screen during printing.
How Mesh Count Affects Print Quality
- Ink Deposition
The mesh count significantly influences the amount of ink deposited on the substrate. Lower mesh counts have larger openings, allowing more ink to pass through, which is ideal for printing bold, solid areas. Higher mesh counts have smaller openings, reducing ink flow and enabling finer detail reproduction. The choice of mesh count depends on the desired ink deposit and the type of design. - Detail Reproduction
The mesh count also impacts the level of detail that can be achieved in the print. Higher mesh counts with finer threads are better suited for intricate designs with fine lines and small text, as they provide more precise control over ink deposition. Lower mesh counts may cause the finer details to appear blurry or distorted due to excessive ink flow. - Ink Types and Substrates
Different inks and substrates may require specific mesh counts for optimal results. For example, water-based inks typically require higher mesh counts to control the ink flow, as they are thinner than plastisol inks. Similarly, printing on rough or absorbent substrates may necessitate a lower mesh count to ensure adequate ink coverage.
Choosing the Right Mesh Count
Selecting the appropriate mesh count involves considering several factors, including the design complexity, ink type, and substrate. Here are some general guidelines:
- Low Mesh Counts (60–110)
Ideal for bold, heavy designs, opaque prints, and thicker inks. Suitable for printing on dark garments, fabric, and textiles. - Medium Mesh Counts (156–230)
Versatile for most standard printing applications. Suitable for medium-detail designs, average ink deposits, and a variety of substrates. - High Mesh Counts (305 and above)
Best for detailed and intricate designs, fine lines, and small text. Suitable for thin inks, such as water-based inks, and printing on paper or other smooth surfaces.
Conclusion
Understanding screen mesh count and its impact on print quality is essential for achieving the best results in screen printing. By selecting the appropriate mesh count based on your design, ink, and substrate, you can control ink deposition, maintain detail accuracy, and produce high-quality prints. At Sias Canada Inc., we offer a range of screen printing equipment and supplies, including custom pre-stretched screens with various mesh counts. Contact us today for expert advice and top-quality products to enhance your screen printing projects!