Optimizing Your Screen Printing Workflow for Maximum Efficiency
Optimizing Your Screen Printing Workflow for Maximum Efficiency
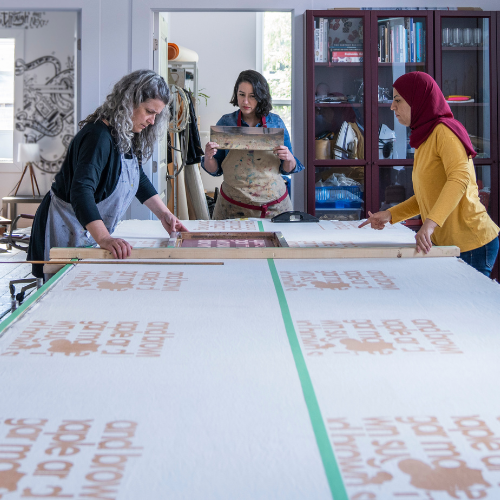
Efficiency in screen printing is crucial for maximizing productivity and profitability. A streamlined workflow not only reduces production time but also minimizes errors and waste, leading to higher-quality outputs. Whether you're a small business or a large-scale operation, optimizing your screen printing process can significantly impact your bottom line. In this post, we'll explore practical tips and strategies to enhance your screen printing workflow, from design preparation to final production.
Design Preparation and Approval
The first step in optimizing your workflow begins with design preparation. Ensure that your artwork is finalized and approved before moving to production. Use design software to create precise digital files, and consider using proofing tools to get client approval on colors and layout. This step prevents last-minute changes and reduces delays.
Efficient Screen Setup
Setting up screens efficiently is vital for a smooth workflow. Organize your screens by size and mesh count, and label them clearly for easy identification. Use automated screen coating machines and exposure units to speed up the process and achieve consistent results. Additionally, consider investing in a Direct-to-Screen (DTS) system, which eliminates the need for film positives and accelerates screen preparation.
Optimized Equipment Layout
The layout of your screen printing equipment can significantly impact workflow efficiency. Arrange your presses, dryers, and other equipment in a logical sequence to minimize movement and reduce bottlenecks. Consider implementing a linear layout, where each step of the process flows naturally from one station to the next. This setup can help reduce transition times and improve overall productivity.
Time Management and Scheduling
Effective time management is key to maximizing efficiency. Create a production schedule that outlines each job's timeline, from screen setup to final curing. Prioritize tasks based on deadlines and complexity, and allocate sufficient time for each step. Use software tools to manage job tracking, inventory, and order processing, ensuring that everything runs smoothly and on time.
Quality Control Measures
Implementing quality control measures throughout the screen printing process is essential for maintaining high standards. Conduct regular inspections at each stage, from screen preparation to printing and curing. Use test prints to check for alignment, color accuracy, and print quality. Address any issues immediately to prevent costly reprints and ensure customer satisfaction.
Maintenance and Troubleshooting
Regular maintenance of your screen printing equipment is crucial for optimal performance. Create a maintenance schedule that includes routine checks, cleaning, and lubrication. Keep spare parts on hand to address common issues quickly. Train your staff on troubleshooting techniques to minimize downtime and maintain a smooth workflow.
Continuous Improvement
Lastly, always strive for continuous improvement. Analyze your workflow regularly to identify areas for enhancement. Gather feedback from your team and clients to understand potential pain points. Stay updated on industry trends and new technologies that can further streamline your process.
By implementing these strategies, you can optimize your screen printing workflow, increase efficiency, and achieve better results. At Sias Canada Inc., we offer a wide range of equipment and supplies to support your screen printing operations. Contact us today to learn more about how we can help you enhance your workflow and achieve your production goals.