Top 10 Tips for Maintaining Screen Printing Equipment
Top 10 Tips for Maintaining Screen Printing Equipment
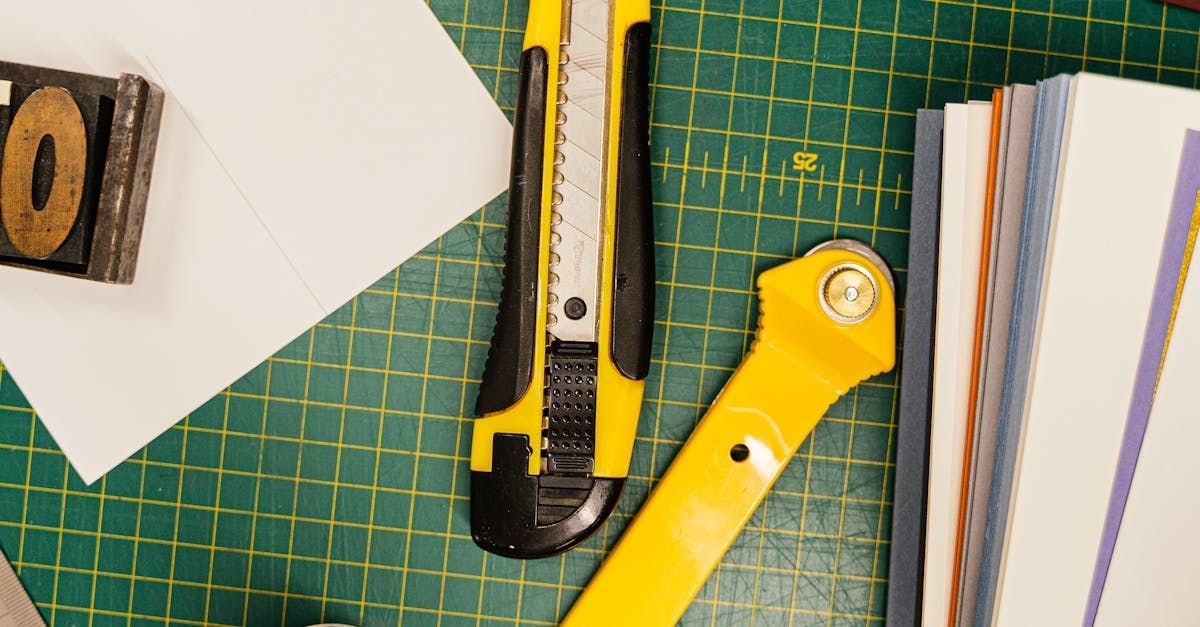
Proper maintenance of screen printing equipment is essential for ensuring longevity, consistent print quality, and smooth operation. Neglecting maintenance can lead to costly repairs, production downtime, and diminished output. To help you keep your equipment in top shape, here are ten practical tips for maintaining screen printing equipment.
1. Regular Cleaning
Regular cleaning is the cornerstone of equipment maintenance. Ink, dust, and debris can build up over time, causing malfunctions and affecting print quality.
- Presses and Screens: Clean screens immediately after use to prevent ink from drying and clogging the mesh. Use screen cleaners or degreasers specifically designed for screen printing.
- Dryers and Flash Units: Wipe down the conveyor belts, heating elements, and exhaust systems. Ensure that no ink or dust accumulates on the surfaces, as this can affect heat distribution and curing times.
2. Lubrication of Moving Parts
Lubricate all moving parts, such as hinges, clamps, and bearings, regularly to ensure smooth operation. Use the manufacturer's recommended lubricants and follow the specified intervals.
- Presses: Check and lubricate all moving components to prevent friction and wear. This is especially important for automatic presses with many moving parts.
- Dryers and Conveyor Systems: Lubricate conveyor rollers and other moving parts to ensure smooth belt movement and prevent jams.
3. Calibration and Alignment
Regular calibration and alignment of your equipment are crucial for maintaining print accuracy and consistency.
- Presses: Check the alignment of platens, screens, and print heads. Misaligned components can cause registration issues and affect print quality.
- Exposure Units: Ensure the light source and vacuum system are correctly calibrated to achieve precise screen exposure.
4. Check Electrical Connections
Inspect electrical connections and components regularly to prevent potential hazards and equipment failure.
- Cords and Plugs: Check for frayed cords, loose plugs, or exposed wires. Replace damaged components immediately.
- Control Panels and Circuitry: Ensure all electrical connections are secure and free from dust and moisture.
5. Monitor and Replace Worn Parts
Keep an eye on components that experience wear and tear, such as squeegee blades, flood bars, and screen mesh.
- Squeegee Blades: Replace blades regularly, as worn edges can affect ink application and print quality.
- Screen Mesh: Inspect screens for tears, holes, or stretched mesh. Replace damaged screens to maintain print sharpness and detail.
6. Maintain a Climate-Controlled Environment
Environmental factors such as temperature and humidity can impact screen printing processes.
- Temperature Control: Maintain a stable temperature in your printing area to prevent ink consistency issues and equipment malfunctions.
- Humidity Control: Excessive humidity can cause inks to dry slowly or affect screen exposure. Use dehumidifiers if necessary.
7. Keep Software and Firmware Updated
For automatic presses and other digital equipment, keeping software and firmware up to date is essential for optimal performance.
- Software Updates: Regularly check for updates and install them to improve functionality and security.
- Firmware Updates: Follow the manufacturer's guidelines for updating firmware to ensure compatibility with new features and equipment.
8. Implement a Preventative Maintenance Schedule
Develop a preventative maintenance schedule to address potential issues before they become significant problems.
- Routine Inspections: Schedule regular inspections of all equipment components, including belts, motors, and sensors.
- Scheduled Maintenance: Follow the manufacturer's recommendations for routine maintenance tasks, such as belt replacement or lubrication.
9. Train Staff on Proper Equipment Use and Maintenance
Ensure all staff members are trained on proper equipment operation and maintenance procedures.
- Operational Training: Train operators on the correct use of equipment, including start-up and shut-down procedures.
- Maintenance Training: Provide training on routine maintenance tasks and troubleshooting common issues.
10. Keep a Maintenance Log
Maintain a detailed log of all maintenance activities, including cleaning, repairs, and part replacements.
- Record Keeping: Document the date, type of maintenance performed, and any parts replaced. This helps track the equipment's condition and schedule future maintenance.
- Issue Tracking: Keep a record of any issues encountered and how they were resolved. This can help identify recurring problems and address them proactively.
Regular maintenance is vital for the smooth operation and longevity of your screen printing equipment. By following these ten tips, you can ensure that your equipment remains in top condition, reducing downtime, and maintaining high-quality production. At Sias Canada Inc., we offer a wide range of screen printing equipment and supplies, as well as expert advice on maintenance and troubleshooting. Contact us today to learn more about how we can support your screen printing business!